Overcoming the manufacturing skills gap in the supply chain
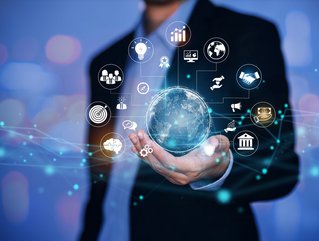
In today's rapidly evolving digital economy, supply chain operations worldwide are embracing digital transformation as a strategic imperative. However, organisations recognise that as technology continues to disrupt traditional supply chain processes, one of the major challenges hindering progress is a lack of core competencies – supply planning, financials, project management, strategy and analytics – and digital savviness among their supply chain professionals.
“The paradigm shift towards digitalisation has become essential for businesses, however, ensuring employees have the right skills to successfully navigate the complexities of digital transformation and embrace technology is key,” says Adrian Preston, Head of Supply Chain Development at Skill Dynamics.
In a recent report by digital training provider Skill Dynamics, 99% say they are leveraging transformative tools such as AI and big data analytics to enhance their processes and drive organisational growth.
“The study also brings to light that despite substantial investment, 25% did not observe any improvements in speed or accuracy,” says Preston.
This disparity between technology adoption and lack of observed improvements highlights that simply investing in advanced tools is not enough; individuals must possess the necessary expertise to leverage them effectively. Despite this, the report found 63% of organisations plan to invest a large amount into digital technologies in FY23 / 24.
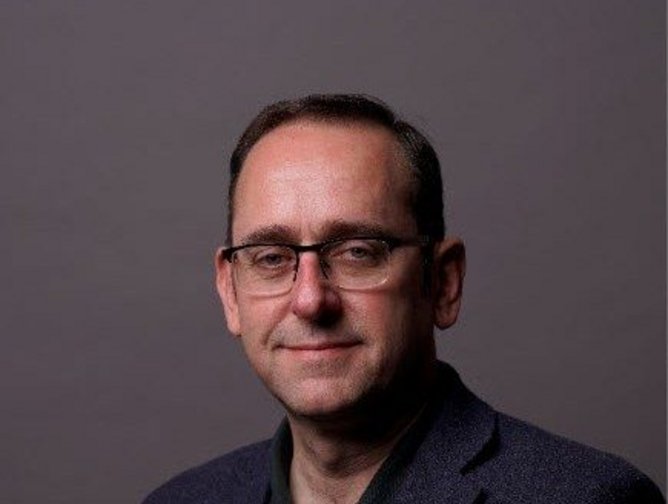
Adrian Preston, Head of Supply Chain Content at Skill Dynamics
Success in supply chain management
Given the global interconnectedness brought about by modern technology, data is now readily available at our fingertips.
“47% of those surveyed said they use digital technologies to manage costs and fluctuations, while 45% of respondents rely on these tools to make informed decisions regarding sourcing support,” says Preston. “But, the true value lies not in the data itself, but in our ability to extract meaningful insights from it. However, reaching the pinnacle of success in supply chain management requires a marriage between experience and training to help professionals in making informed decisions that drive operational excellence and business growth.”
According to Preston, we often find ourselves with two camps of people:
- Senior professionals who possess foundational knowledge of supply chain principles, such as forecasting, inventory management and supply planning, but lack digital skills
- Junior professionals who excel in digital know-how but lack the vertical expertise in core supply chain competencies
“39% of professionals believe that their team members are not using all digital technologies to their full potential because they lack clarity on when or why it should be used,” says Preston. “Bridging this gap is paramount to achieving supply chain excellence. For instance, when determining safety stock, it is essential to consider not only demand variations but also variations in supply. Merely relying on data and IoT capabilities can lead to inaccurate outcomes.”
Therefore, a convergence of expertise is necessary. According to Preston, both senior and junior professionals must undergo training to enable the transfer of skills across the field to facilitate a holistic and integrated approach to supply chain management.
“The importance of possessing core competencies and digital skills cannot be overstated, as the consequences of lacking them can be disastrous for organisations,” he says. “Without them, the perilous tale of Neanderthals becomes an analogy of falling behind in the journey of evolution. It serves as a cautionary tale, to avoid being left behind and ultimately ceasing to exist, organisations must prioritise the acquisition of digital skills and combine them with the necessary competencies to transform data into actionable insights.”
Empowering professionals through training
The key to harmonsing skill sets truly lies in getting training right. Traditional training has been sporadic, occasional and expensive, often involving long periods away from work and delivering minimal value.
“Now, one effective strategy is to adopt a modular and flexible approach, enabling individuals to learn in small, manageable chunks that align with their specific needs and schedules,” says Preston. “E-learning platforms, like Skill Dynamics, received strong support from 52% of respondents, recognising the need to offer the flexibility that modern professionals seek, empowering them to acquire knowledge at their own pace.”
Whether it's within the workplace, factory, or across nations, striking a balance between IT literacy and core skills for successful digital transformation as such, shifting from reactive to proactive approaches that mitigate risks, errors and unseen costs.
“While digital technologies optimise supply chains, the magic happens when human expertise and collaboration ignite a spark of innovation and deliver real value.”
- SAP’s AI Joule set to Transform Supply Chain ManufacturingAI & Automation
- Top Ten: Diverse Companies in ManufacturingProduction & Operations
- How Smart Factories are Reshaping the Manufacturing SectorSmart Manufacturing
- Crowe UK: 2024 Manufacturing Outlook Report Explores GrowthProduction & Operations