Top 10 Lean Manufacturing Tools
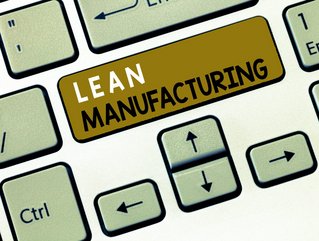
Lean manufacturing focuses on advancing productivity and lowering the volume of waste. Cases of successfully implemented lean manufacturing can save time across the manufacturing process and still create a top quality product.
Lean manufacturing tools can help manufacturers improve quality, productivity, efficiency and customer satisfaction across their manufacturing operations.
There are many businesses which keep lean manufacturing ideas at their core. Nike, Toyota, Ford, TMP Solutions, Nissan, Domino Printing, Unipres Ltd, John Deere, Caterpillar Inc. & Parker Hannifin are our Top 10 lean manufacturers.
Read on to hear all about our Top 10 Lean Manufacturing Tools:
10. Value Stream Mapping (VSM)
For those manufacturers who want to visualise their operations and reduce time spent on tasks, Value Stream Mapping (also known as VSM) is a tool which can help to do this.
The origins of VSM are unclear, but it is believed that the technique comes from Toyota Motor Corporation, where it is also known as Material & Information Flow (M&I). The company currently offers training courses in the subject.
9. Total Productive Maintenance (TPM)
TPM looks at increasing equipment effectiveness and encourages operators to take true ownership of maintenance tasks. TPM aims to achieve zero breakdowns in production, to speed up running, eradicate defects and create a safe working environment. This shared responsibility can reach the goals of lean manufacturing - freeing up time, minimising cycle times, ensuring that there are no accidents and no defects get through.
8. Kanban System
To better manage a manufacturing workflow, manufacturers can use the Kanban System. Kanban translates to ‘visual card’ in Japanese and was first used by Toyota. It’s a visual signalling system which ensures that materials are restocked after being used. This is designed to minimise waste and prevent excess stockpiles.
7. Poka-Yoke
Another form of Japanese quality control, this technique was also developed by engineers at Toyota. Poka-Yoke translates to ‘mistake-proofing’ and reduces the volume of defective items in the manufacturing process from human error. This is done by making sure every step of the process takes place in a secure manner and detects errors before they occur.
6. Just-in-Time (JIT)
JIT focuses on producing exactly the amount needed at the point where customers most require it, bringing together raw-material orders from suppliers and production schedules. Incoming goods are only received at the time when they are needed. While advantageous to manufacturers, there are some key considerations and best practices to follow that will enable JIT to provide value.
5. Kaizen
Kaizen encourages continuous improvement across company culture, leadership, processes, productivity, quality, safety and technology. It ensures that every employee, regardless of position in the hierarchy, can suggest ideas for process improvement. While every opinion won’t result in a major change within an organisation, over time, small improvements will add up and lead to significant reductions in wasted resources.
4. Standard Work
Standard work is a repeatable work method designed to meet customer requirements. It reviews the people, methods, materials and equipment needed for a task and then sets out the steps, time required and expectations for this. Standard Work documents can be used to observe and improve the work.
3. Single-Minute Exchange of Die (SMED)
The technique behind SMED is to minimise setup or changeover time in manufacturing, which advances flexibility by streamlining operation. When applied correctly, SMED should only take ‘single-minutes’, that is, under ten minutes. SMED has a range of benefits such as lowering costs, improving responsiveness to customer demand and smaller inventory.
2. 5S
With 5S, the goal is to keep a workplace clean and efficient. Also developed by Toyota in the 1950s, there are five principles:
Sort: Manufacturers should sort through the items in a factory and decide which are no longer useful and can be removed.
Set in Order: Once the sorting has been completed, manufacturers should set the remaining items in order of usefulness.
Shine: Oh yes, it’s time to clean all the items.
Standardise: Once everything is clean and organised, make sure that it stays that way.
Sustain: Keep the momentum going. When new employees arrive, make sure that they receive training on 5S.
1. Continuous Flow
A manufacturer is nothing without its customers and Continuous Flow is designed to increase their loyalty, by delivering the right value at the right time. The principle encourages the uninterrupted movement of items through production, with the aim to reduce bottlenecks and delays.
Dissimilar to popular batch processing, Continuous Flow moves one product through the steps of the manufacturing process, instead of keeping the items in batches. This allows products to be brought continuously, which creates quicker delivery to customers. Another benefit of Continuous Flow includes a lower volume of waste, which is a tenant of Lean Manufacturing. This tool was also developed by Toyota.