
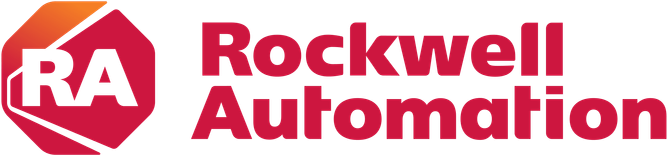
10. Rockwell Automation
Rockwell Automation builds control systems that enable real-time monitoring to help streamline operations and minimise downtime.
This digitalisation journey includes working with robots, combining the physical with the virtual and using AI to spot potential failures.
Mondeléz International has partnered with Rockwell Automation for years for this purpose.
"The scope of our project in North America focuses on our Integrated Digital Factory, which includes assessment and remediation for infrastructure readiness, such as machine performance data and reporting," explained Mondeléz’s Bob Pegher.
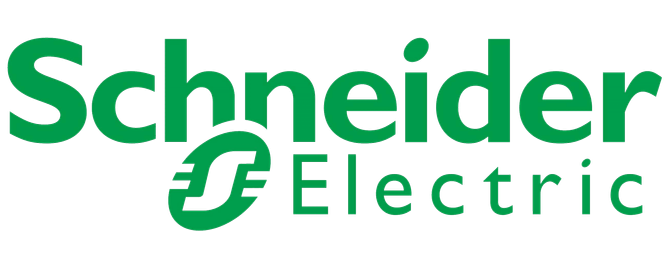
9. Schneider Electric
Schneider Electric is on a mission to empower its customers to make the most of energy and resources, to advance sustainability. The company has partnered with Accenture to develop Schneider Electric Digital Services Factory. With new capabilities such as analytics, Schneider Electric will be able to bring new services to market much faster.
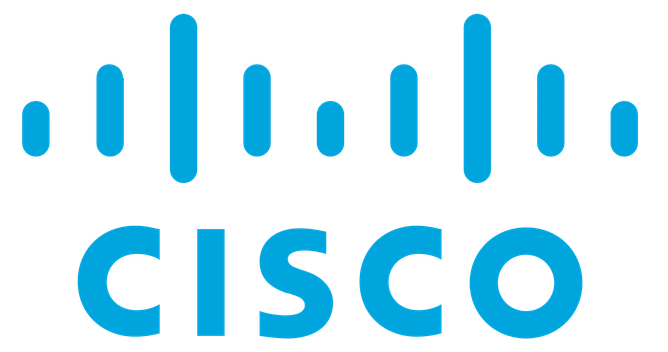
8. Cisco
Cisco was founded in 1984 by a team of Stanford University computer scientists, who wanted to help people make powerful connections. Now, Cisco’s networking and connectivity solutions allow digital factories to improve their security. Cisco’s networking solutions support the connectivity needed for secure cloud computing.
“At Cisco, we’re delivering the digital factory as a trusted partner for hundreds of manufacturing customers – and more than 50,000 customers across all industries, around the world,” said Liz Centoni, Executive Vice President, Chief Strategy Officer and General Manager, Applications at Cisco.
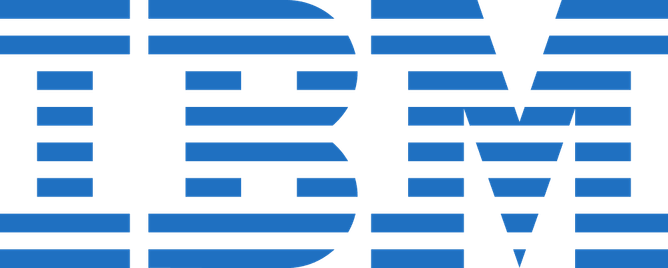
7. IBM
IBM was founded in 1911 and remains one of the world's biggest IT companies. The company offers solutions for smart manufacturing that leverage AI, IoT and advanced analytics. Vehicle manufacturer Toyota uses IBM Maximo Health and Predict in its digital factory.
“Leveraging shop floor data powered by AI and IoT can come together to reduce downtime by 50%, reduce breakdowns by 70% and reduce overall maintenance costs by 25%,” explains Rafi Ezry, Managing Partner US Industrial Market at IBM Services.
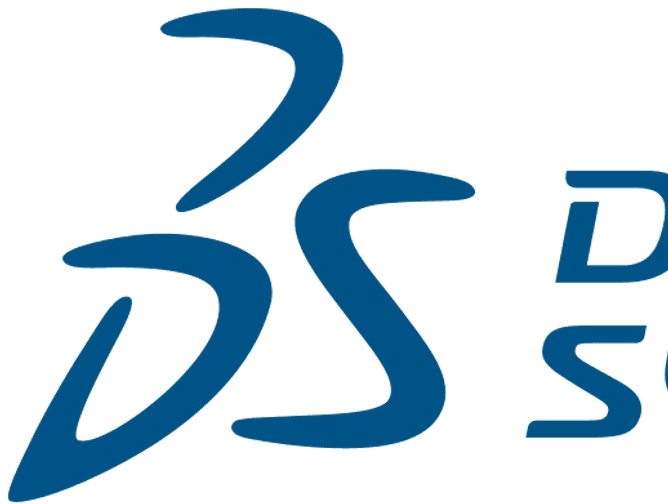
6. Dassault Systèmes
Dassault Systèmes is known for its sustainable innovations and is dedicated to reaching climate neutrality by 2040. Digital factories will help them achieve this, through the method of Manufacturing Execution Systems (MES), a system that monitors goods from a raw material to a final product. Using Dassault Systèmes’ MES, manufacturers can standardise production processes from one plant to another, enable real-time data-collection, advance quality control and integrate with ERP systems.
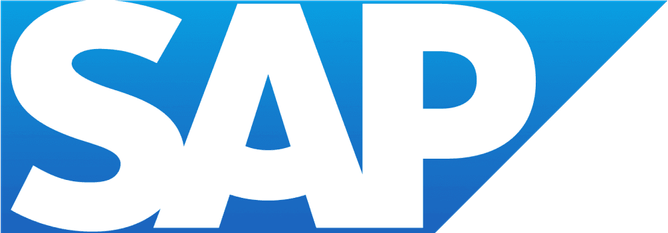
5. SAP
SAP is a software development company that offers customers a sustainable supply chain with its manufacturing software. SAP uses digital twin technology so that manufacturers can see a replica of their physical assets. Using IoT, SAP integrates its devices and sensors to enable data collection from machines allowing for top process optimisation.
SAP also offers cloud-based services to digital factories, which lets customers use flexible computing resources in tasks, such as advanced analytics.
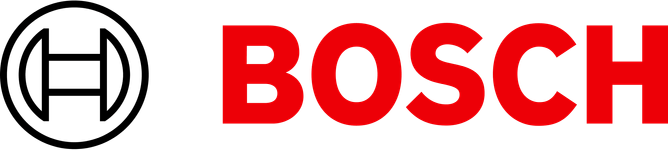
4. Bosch
The Bosch Group supplies a range of services and technologies, which are divided into four business sectors: Mobility Solutions, Industrial Technology, Consumer Goods and Energy and Building Technology.
Bosch uses Industry X to advance digital transformation in its robotic solutions and IoT to connect machines, devices and systems, which enables data collection, analysis and communication.
In Bosch’s Mobility Solutions, drivers benefit from advanced safety, comfort, convenience provided by Connected Horizon from Bosch, which uses cloud-based services to keep drivers safe.
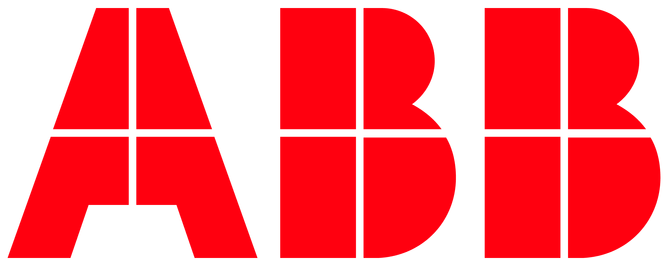
3. ABB
ABB is building a more sustainable manufacturing future, especially in its robotics, electrification and industrial technology production. In September the company announced that it is investing US$280m to build a new ABB Robotics European Campus, in Västerås, Sweden, which will double ABB’s robot production capacity.
“In our new R&D centre, we are focusing on the development of new digital and AI-enabled technologies, making robots increasingly accessible while lowering the entry barrier for applications in all industries,” said ABB Robotics president, Marc Segura
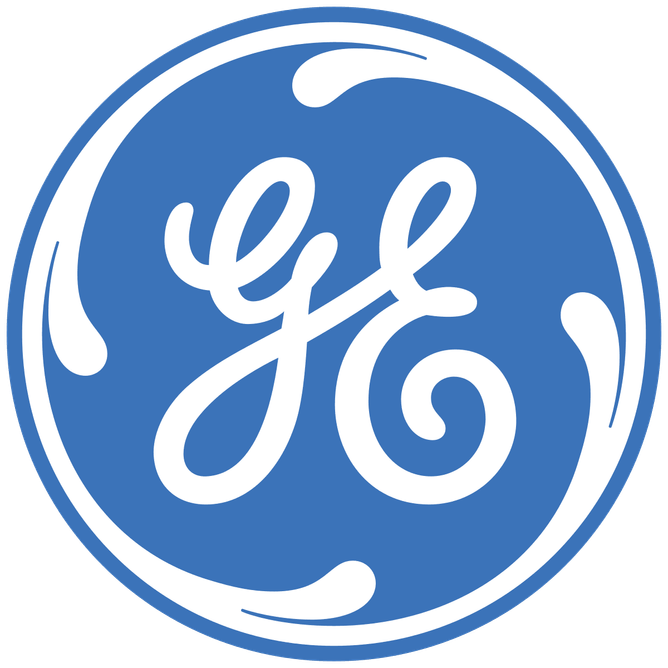
2. GE
Digital solutions innovator GE aims to help their customers make better informed decisions, using GE’s intelligent devices, data analytics and applications. The company utilises Industry X to advance digital transformation and innovation across its manufacturing.
At GE, digital twins are a core part of digital transformation. GE Digital’s Chief Technology Officer, Colin Parris, founded and heads the Digital Twin Initiative in GE and is a board member of the Digital Twin Consortium.
“A digital twin, for me, is a living, learning representation of some form of asset or system. 'Living' means there is a continual stream of data that allows the model to be aware of the environment. There's also feedback data,” which is invaluable, he explained.
Due to the strong reliance on connectivity, digital factories need their cybersecurity to be top-notch to protect them from any possible threats. GE Research’s cybersecurity team is at the forefront of this, protecting the company, its employees and customers.
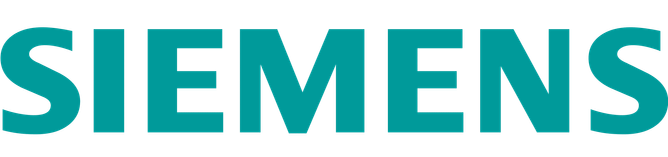
1. Siemens
Siemens is a big name in digital manufacturing, building the software and hardware needed by various industries. The company is focused on building strong supply chains, smarter buildings, clean and green transportation and a more resilient healthcare sector. Siemens actively utilises Industry X to drive digital transformation in many ways and in particular, in the manufacturing sector.
Brian Holliday, Managing Director of Digital Industries at Siemens, recently discussed how digital twins are expanding the potential of the metaverse.
“It’s been really exciting to see high definition graphics and a really immersive experience, put together with a physics based model. Whilst not at the quality of gaming graphics, the digital twins created lifelike, physics-based models from production lines.”
Using an array of modern technologies, Siemens provides advanced digitalisation solutions for manufacturing processes in its digital factories, allowing for improved efficiency and enhanced product quality.