Markforged Among Firms Embracing Distributed Manufacturing
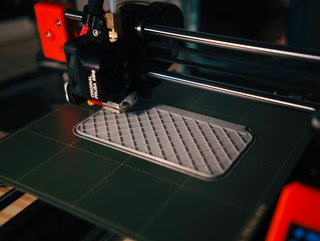
Globalisation in the 2010s was spoken of as an economic inevitability, an unstoppable market force that consumers and companies alike simply had to adjust to.
But today, amid the rise of localised production, things appear to be changing. For manufacturers with a digitised supply chain – like 3D printing firms – it’s a development that suits them perfectly.
Distributed manufacturing: What it is and its impact on the manufacturing supply chain
Also termed ‘decentralised manufacturing’ and ‘local manufacturing’, distributed manufacturing is the production of goods close to the point of use.
According to HP’s Digital Manufacturing Trends Report, 52% of companies were looking into localised production in 2021. That number is even higher today. Manufacturer investment into this model has been driven by a range of political and environmental factors.
- Continuous trade wars and tariffs that compromise global supply chains have swayed manufacturers to move production nearer to consumers.
- Concern over climate change has made reducing long-haul shipping a sustainability goal for many, a goal which also addresses the dramatic increase of energy prices.
- Localised manufacturing also ensured the continuity of many businesses during COVID-19,inspiring others to invest closer to home in anticipation of future global pandemics.
- Localised manufacturing is even used by businesses as a major selling point, encouraging customers to purchase and invest in their local economy and community.
However investment is not only driven by risk mitigation and climate commitments. Companies also recognise that distributed manufacturing has its own distinct advantages compared to traditional manufacturing models. Traditional models are based on the premise of identical, high-volume production, a system which doesn’t account for the growing trend towards customisability, faster turnaround times and more efficient supply chains.
Distributed manufacturing offers something very different. A digital network of decentralised production sites, spread across locations, connected by digital technology. It provides superior flexibility and agility, opening the door to faster delivery, sustainability, customisation and support for regional markets. And it’s been prominently adopted in specific areas of manufacturing like 3D printing, where customisability reigns supreme.
3D Printing: Putting distributed manufacturing on the map
3D printing – along with robotics, data analysis and the Internet of Things – is one of the key technologies facilitating distributed manufacturing.
It works by creating a model in CAD which is then converted into two-dimensional layers. This file is then sent to a 3D printer that painstakingly crafts the three dimensional object layer by layer. With a highly digitised process and low reliance on physical tools, 3D printing technology is well suited to driving the transition to distributed manufacturing.
It accelerates lead times by directly producing end-use parts and by reducing the time to market by speeding up prototyping rates. Because 3D printing doesn’t rely on injection moulds, which typically take time to produce and set, production can start immediately after receiving orders. This takes production times from a few days to mere hours.
Distributed manufacturing also helps the 3D printing industry reduce warehouse costs, by reducing their number of sites and even switching to digital inventories. These inventories contain a centralised virtual storage unit for 3D designs in addition to producing parts when customers need them and sending data between facilities. This all helps bypass the need to maintain and protect a physical inventory.
In addition to all this, distributed manufacturing bolsters one of the biggest benefits of 3D printing: its ability to provide on-demand manufacturing. It allows the industry to rethink the entire concept of warehousing, replacing what is an inefficient and unnecessary ‘made-to-stock’ order model.
Markforged is a leading industrial 3D printing company that has extensively supplied US army and naval operations.
Its CEO Shai Terem, who has led the movement of 3D printing to digital source platforms, says: “I think the first step, which we’re seeing, is a lot of construction for manufacturing. But it’s a long process. So, I think the last few years just showed how supply chains are broken, and that businesses must do something differently.
"This is why we have the opportunity now to really help our customers, to really help these manufacturers build resiliency and flexibility in their own supply chains. And it’s not for money that’s going to come tomorrow — it’s a long journey, over the next 10 or even 20 years.”
This move creates some additional considerations for 3D printing companies. By digitising their supply chain infrastructure they increase their cyber security vulnerabilities, giving gangs more opportunity to extort their data and seriously compromise their entire operation. To remedy this, 3D printing companies must renew investment in cyber security and employee training.
******
Make sure you check out the latest edition of Manufacturing Digital and also sign up to our global conference series - Procurement & Supply Chain 2024 & Sustainability LIVE 2024
******
Manufacturing Digital is a BizClik brand.