How Digital Twins are Transforming Product Manufacturing
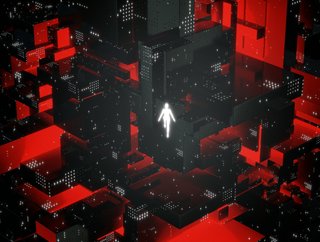
A company's longevity hinges on many factors. A major one in 2024, as companies compete to retain customers and dominate a fast-paced attention economy, is the ability to develop and launch new products.
Consistent product innovation and enhanced quality is no longer a selling point, but a consumer expectation – and a necessity in order to remain competitive.
Products must constantly be updated with performance improvements, new features and the integration of novel technologies. They also need to meet rising sustainability concerns in their design, material and manufacturing process. This is all happening while companies endeavour to keep research and development costs low, stretching their resources and teams.
Or, rather, this is how product development happened before the introduction of digital twins.
What are digital twins and how can they enhance supply chain manufacturing?
A digital twin is a virtual replica of a system’s behaviour in its operating environment. That system can be a supply chain, a manufacturing process or even just a singular product, all of which are represented by a collection of digital models. When products are systems, they are physics-based simulations designed to match the characteristics of their physical counterparts. They give companies the power to modify products in a virtual space, without the same costs, time and risks involved with testing in the real world.
Digital twins can provide 360-degree views of customers, consolidating their demographic, behaviour and payment methods to offer predictive suggestions on new product development. They can replicate the operation of real-world assets and processes, like critical pieces of factory machinery and entire factory production lines.
Crucially, digital twins are being used for product development by a diverse range of manufacturers to enhance customisability and efficiency.
Rolls-Royce and Össur benefit from digital twins
A pivotal industry where digital twins are being utilised is auto manufacturing.
Already, around three-quarters of auto manufacturers use them as part of their development process to assist how they design, develop, monitor, fix and even build their vehicles. Ford is one such example, using digital twins to develop their self-driving cars and test their products under various driving scenarios.
Rolls-Royce is also using digital twins in its IntelligentEngine programme to simulate engines and gather information on their performance, allowing teams to predict maintenance and reduce downtime. " Digital "O" origins start with the traditional engineering "V" framework." Terry Hegarty, Head of Digital Capability & Innovation at Rolls-Royce, said. " If you take a mirror image of that, you end up with a shape that is a diamond. The top half of that diamond is the digital representation of that physical world. What we've done in Rolls-Royce is taken the diamond and we've actually made it an O shape. And the reason we've used an O shape is that it's a continuous process that exists through life, through our products, from early design all the way to our end product and end of operation."
Healthcare is another industry innovating with digital twins. Össur, a global prosthetic and orthopaedic solutions provider, is using the technology to design and manufacture custom-made prosthetics. This ensures optimal functionality and a tailored fit for each patient, creating virtual models that the company’s engineers and designers can use to simulate and analyse various design iterations.
There’s also the SimCardioTest funded by the European Commission, which uses digital twins to replicate the human heart. These models will help the medical field better diagnose, detect and treat heart-related illnesses, by conducting tests that avoid the costs and ethical considerations involved in human medical trials.
While there are challenges associated with digital twins, including how complex they can become and how specific their data needs to be, it's clear they are creating incredible new opportunities for innovation and enhancement in the manufacturing industry.
Product development is one of the biggest areas they can enhance and leaders are rushing to invest in the concept. The global market for digital twin technologies is forecast to grow at about 60% annually over the next five years, reaching US$73.5bn by 2027.
******
Make sure you check out the latest edition of Manufacturing Digital and also sign up to our global conference series - Procurement & Supply Chain 2024 & Sustainability LIVE 2024
******
Manufacturing Digital is a BizClik brand